Proximity sensors are used to detect the presence of an object without any direct contact. It is used as an alternative to the limit switches. There are various types of proximity sensors available in the market. Their invention led to a revolution in the field of industrial automation and robotics. Proximity switches were developed by Wilfried Gehl, Walter Pepperl, and Ludwig Fuchs. They are used in with process controllers such as PLC and DCS for process automation.
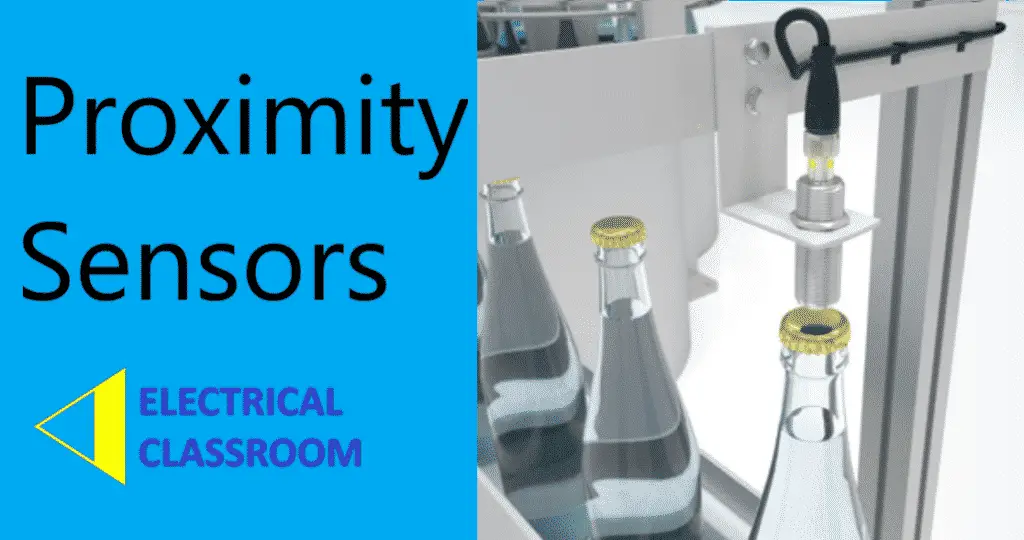
What is a Proximity sensor?
A proximity sensor is an instrument which can easily sense-object without having any physical interaction or contact.
The mechanism involves an emitting electromagnetic field, light, or ultrasonic sound which allows it to look for any unusual activity or change in the field and finally return the signal. The object being sensed usually depends on the proximity of the sensor, in simple terminologies, the type of object being sensed.
There is a wide range of sensors available in the market. The selection of which depends on the object to be sensed and the sensing range. Since there are no mechanical parts in it, a proximity sensor is very durable and can last longer than the conventional limit switches.
Types of Proximity sensors
There are five major types of proximity sensors.
- Inductive proximity sensor
- Optical proximity sensor
- Capacitive proximity sensor
- Magnetic proximity sensor
- Ultrasonic proximity sensor.
Inductive Proximity Sensors
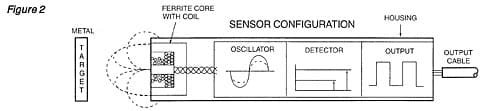
Inductive proximity sensors work on the principle of Faraday’s law of electromagnetic induction. These sensors can be used to detect metallic objects only. The mechanism involves an inductive coil and oscillator that produces an electromagnetic field. When any metallic object comes in the range of the sensor eddy currents are set up in the object. This results in the variation of coil inductance. A monitoring circuit present in the sensor detects variations in inductance caused due to the eddy current that is generated on a conductive surface and triggers the output contacts.
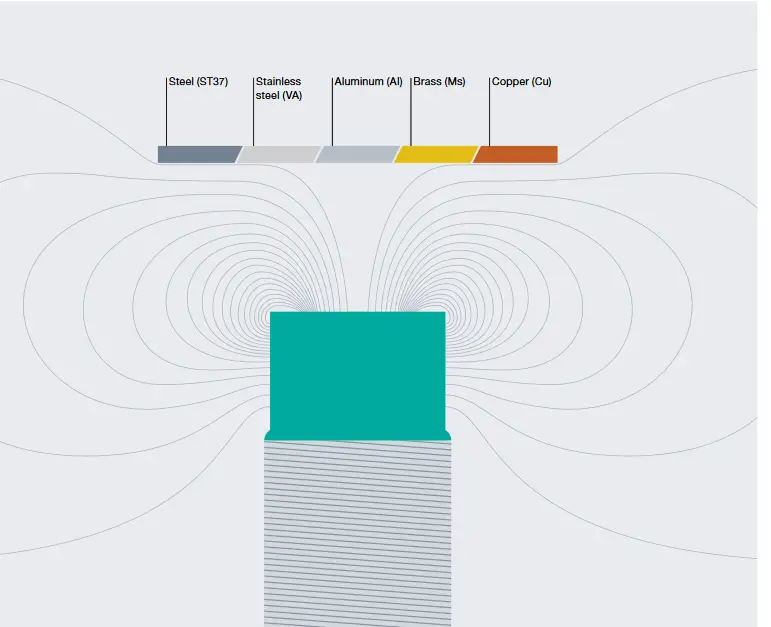
Inductive sensors have a short sensing range. They are used in metal detectors, brush holders, and dryers in car washes, bottling plants, machine tools, motorized valves (to sense valve open/close status), and other industrial applications.
Optical Sensors
Optical proximity sensors use light to detect objects. They use any one of the following methodologies: through beam detection, retro-reflective beam detection, and diffused beam detection.
Through-beam sensor: It consists of a transmitter and a receiver located in a straight line such that the light from the transmitter falls directly on the receiver. Whenever any object coming between the transmitters and receiver blocks the light beam and the receiver triggers the output contacts. Through-beam sensors have a long sensing range and high operational reliability.
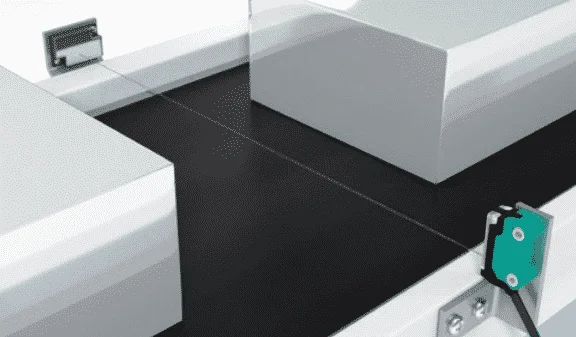
Retro-reflective beam sensor: It consists of a transmitter and a receiver housed in the same unit. The receiver detects the beam reflected back from the reflector and triggers the output contact whenever any object interrupts the detection. Retro-reflective beam has a shorter sensing range than through-beam sensors. The biggest disadvantage is that only highly polished objects can act as reflectors.
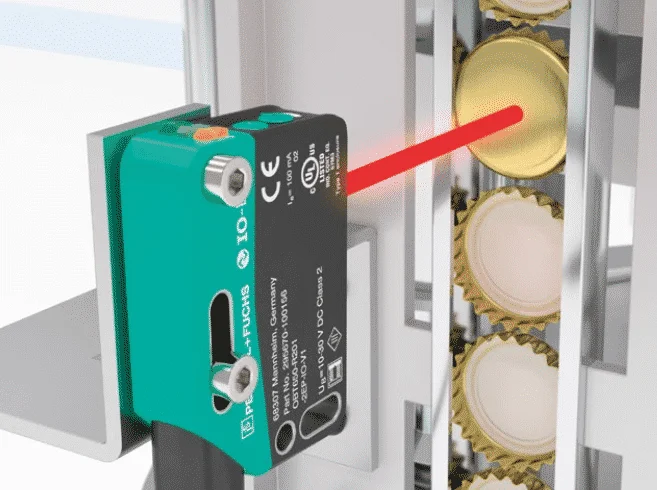
Diffused beam sensor: As with retro-reflective beam sensors, diffused beam sensors consist of the transmitter and receiver housed in the same unit. The receiver detects the reflected beam and triggers the output contact on the detection of reflected light. The diffused-beam sensors do not require any separate reflectors.
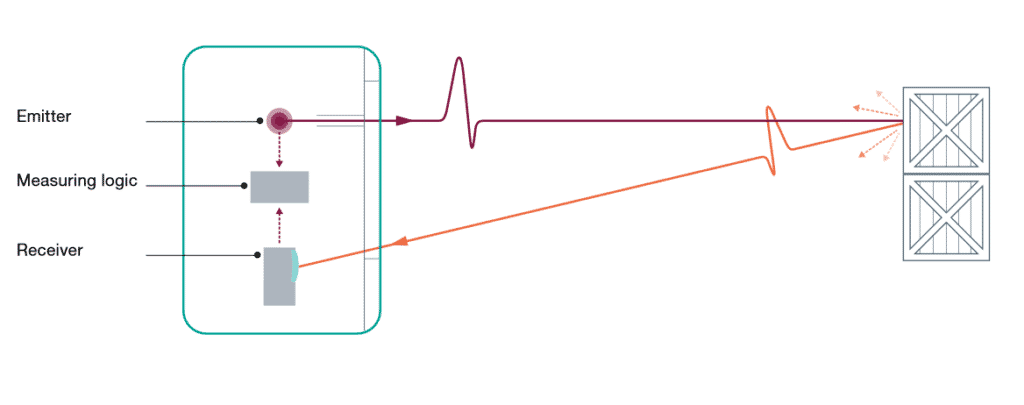
Capacitive Proximity Sensors
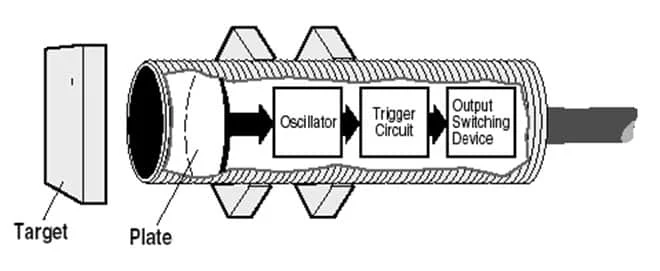
Capacitive proximity sensors can be used for metallic & non-metallic objects and substances without any limitation to the state (except for gas). The capacitive sensors can detect the object in any state, powder, granule, liquid, and solid form. As the name suggests, it works on the principle of capacitance, by sensing the variation in capacitance. The amount of capacitance depends on two things, distance and the size of the targeted object.
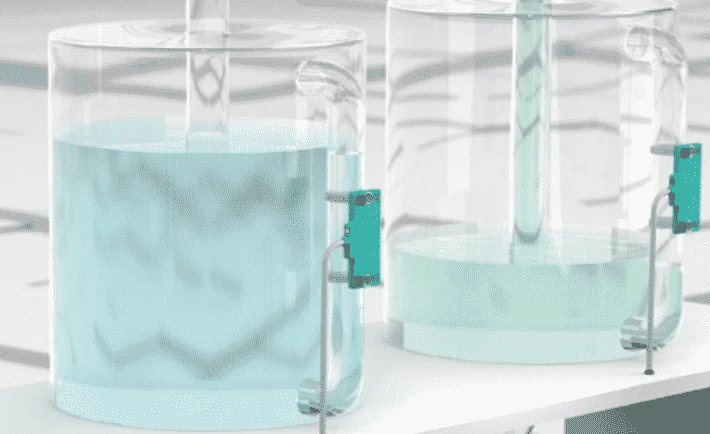
The capacitive proximity sensors have circuits the same as that of inductive sensors, but the electromagnetic coil is replaced by metal electrodes. The electrode in the sensor acts as one plate of the capacitor while the target acts as the other plate of the capacitor. The air gap between the two functions as the dielectric. When the target enters the sensing range and the target changes the capacitance of the oscillator and the oscillations increase. The change oscillations change the state of the Schmitt trigger which in turn triggers the output contacts.
Capacitive sensors can be used to sense metals, liquids, granules, paper, wood, etc.
Ultrasonic sensor
Ultrasonic proximity sensors have a transmitter and a receiver in the same housing. The transmitter emits high-frequency ultrasonic that hits the targets and reflects as the sonic cone. The reflected waves are sensed by the receiver. Ultrasonic sensors are many applications due to their long sensing range. It can be used for sensing clear glass and plastics. It can be found in robots, automobiles, distance-sensing equipment, etc.
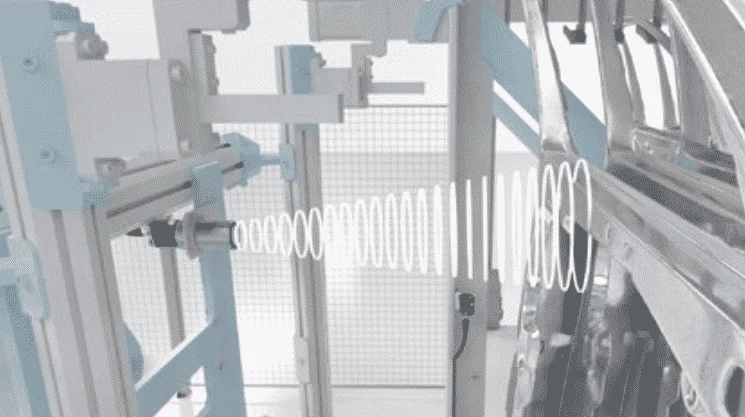
Magnetic Proximity Sensors
A magnetic proximity sensor uses detects magnetic materials. It contains a reed switch inside, that is activated.
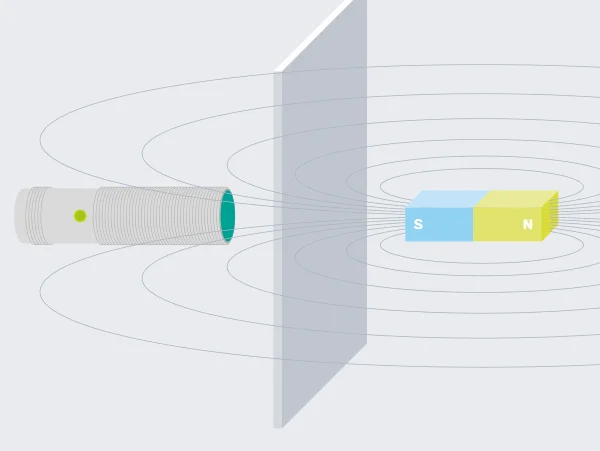
Applications of each type of proximity sensors
There are several types of proximity sensors available in the market. They are used in various aspects of life, their general application is for, detecting objects, counting pieces, measuring velocity, determining the direction of movement, monitoring tools, etc. They are used in smartphones and tablets.
Inductive sensor application includes machine assembly line, the automotive industry, detection of metal parts in harsh conditions.
The optical proximity sensor is used in carton counting, product sorting, and contrast detection.
Magnetic sensor application includes security and military purposes for object detection. While capacitive sensors have multiple uses, the specific ones are; final and thorough inspection of the packaging and precise measurement of the level of liquid or granules filling through walls of plastic or glass tanks.
Of all the applications, one of the major uses of the ultrasonic sensor is to detect the depth of the cavity.
i’ve been working with machine that use this kind of sensor and your article describe many type of proximity sensor.thanks for the information