An electric motor is an energy transformation machinery. It transforms electrical energy into mechanical energy. In other consumes electrical energy and delivers mechanical energy in the form of rotations.
For example, an electric fan consists of a motor that draws electric energy from the mains and delivers kinetic energy (mechanical energy) in the form of airflow. During the transformation, a small amount of electric energy is lost in the form of heat.
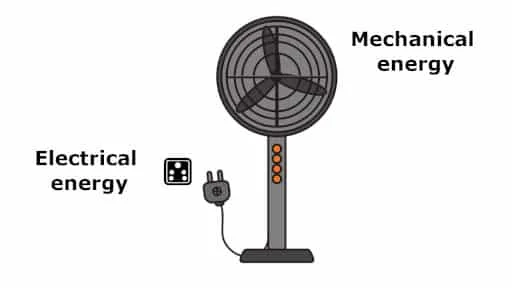
The U.S. Department of Energy (DOE) data reveals that electric motors consume more than 50 percent of all electrical energy in the United States [reference]. Also, the power consumed by the motors accounts for 85% of the total power consumed by industries.
How it works?
A motor shaft spins as a result of interaction between two magnetic fields: One produced by the electromagnet at the stator and the other by the electromagnet at the rotor.
In the case of an AC motor, a rotating magnetic field is produced at the stator when 3 phase power is applied while the rotor field is stationary. Hence, the North pole of the rotor field constantly gets attracted towards the South pole of the stator field and vice versa. Likewise, similar poles of the rotor and the stator repels.
In the case of a DC motor, the stator field remains stationary and the rotor field is changed by changing the direction of current from in it using a commutator. Hence, the North pole of the rotor field constantly gets attracted towards the South pole of the stator field and vice versa. Likewise, similar poles of the rotor and the stator repels.
Classification of electric motors
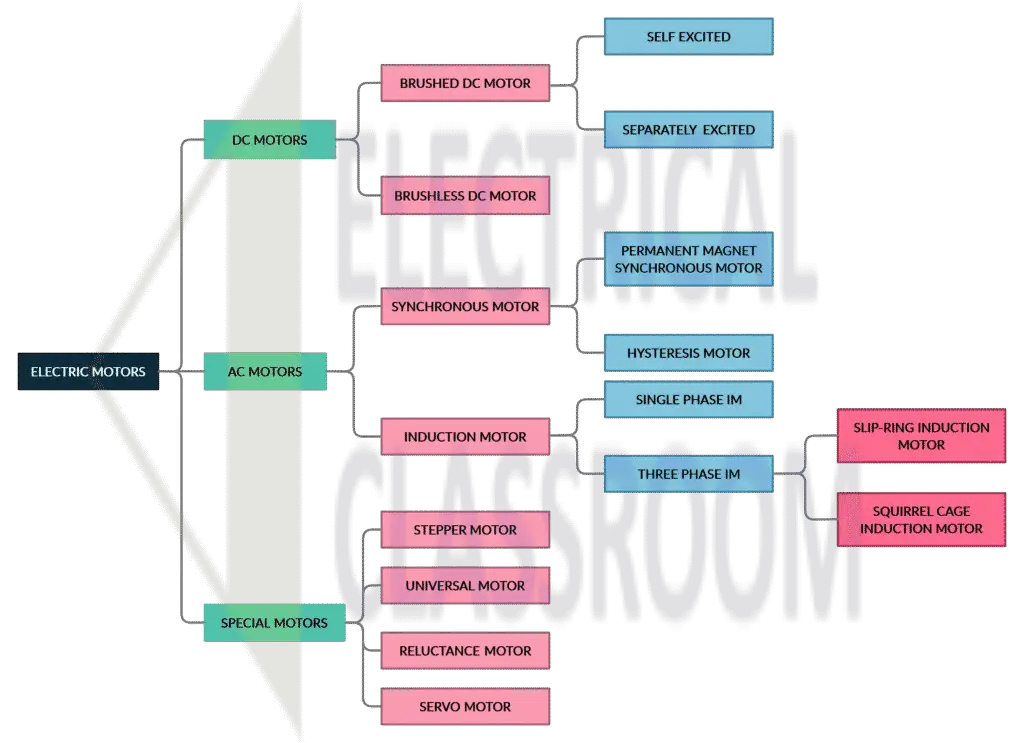
Brushed DC motor
In brushed DC motors armature is present in at the rotor and carbon brushes are used to supply power to the armature. Commutators are present at the rotor to change the direction of current flow.
Brushless DC motor
A brushless DC motor has a permanent magnet at the rotor and a semiconductor switched at the stator. Semiconductor switches convert the input DC supply to pulsating DC to generate maximum torque at a given speed.
Synchronous motor
As the name indicates, the speed of rotation of a synchronous motor remains synchronized with the frequency of applied supply voltage. Three-phase AC voltage is applied to its stator. The rotor consists of a permanent magnet of a coil that acts as an electromagnet when excited. Synchronous motors are not self starting. It requires an external prime mover to accelerate the motor near to its synchronous speed.
Induction Motor
Induction motors are AC motors, in which the rotor is magnetized by the electromagnetic field of the stator. They do not require a supply to the rotor. It is the widely used industrial motor.
Stepper motor
Stepped motors are pulse driven motors used for position control. These motors can move through a specific angle for each control phase applied. They do not require position sensors.
Universal motor
Universal motors can operate with both AC and DC power supplies. They are capable of rotating at high speeds and can be used in blow driers and vacuum cleaners.
Servo motor
Servomotors are used for precise position control. They are brushless DC motors combined with position sensing devices such as encoders and potentiometers. Servo motors are used for closed-loop position control. They find their application in marine navigation, automatic machine tools, air crafts, robots, speed governors, etc.
Motors do not transformer all the supplied electric energy to mechanical output. A small amount of energy is lost during the transformation in the form of heat.
Input power = mechanical output + loss
nice post